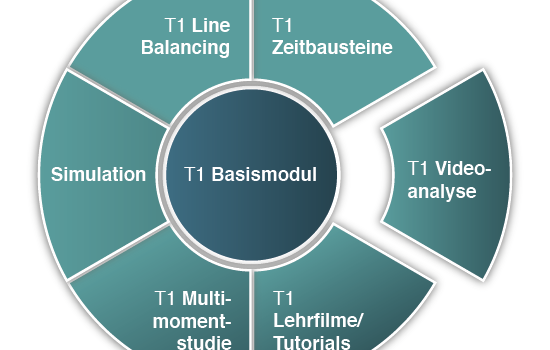
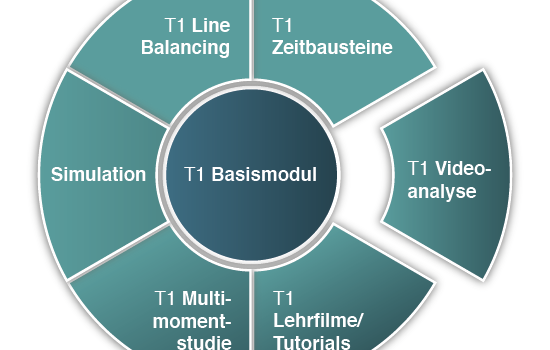
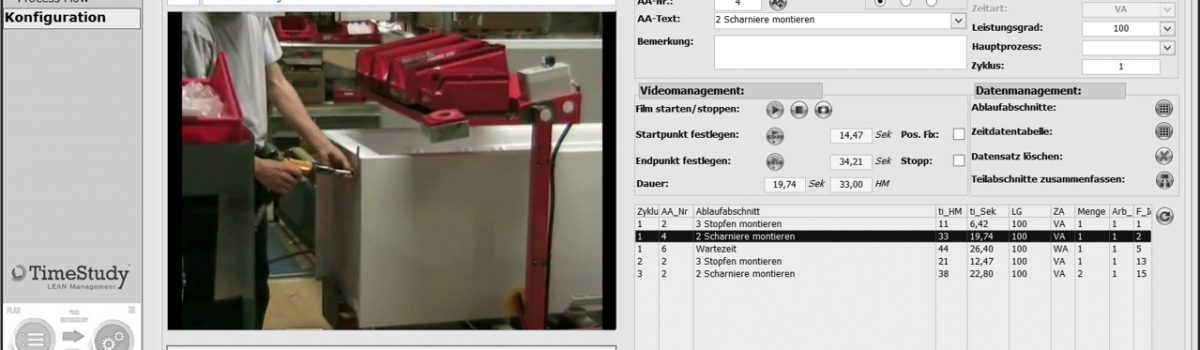
Produktionsoptimierung mit der TimeStudy Videoanalyse
Bei der Produktionsoptimierung mit der TimeStudy Videoanalyse ist die Videoanalyse kein Medium zur Überwachung, sondern sie dient der Optimierung der Produktionsabläufe. Die Produktionsoptimierung ist eine Methode zur kontinuierlichen Verbesserung (KVP) der Prozess- und Produktqualität und ein unverzichtbarer Bestandteil eines betrieblichen Qualitätsmanagements. Die Videoanalyse hilft dabei durch Visualisierung die einzelnen verbesserungswürdigen Schritte aufzudecken, z. B. durch Rüstanalysen oder die Aufnahme und anschließende Auswertung von Produktionsabläufen im Team.
Schlanke Prozesse, eine hohe Produktivität und wenig Verschwendung sichern die Wettbewerbsfähigkeit des Unternehmens. Damit das so bleibt, müssen die Prozesse gemeinsam mit den Mitarbeitern von Zeit zu Zeit angepasst werden. Diesen Prozess vereinfacht die TimeStudy Videoanalyse. Denn die Potentialanalyse für die Prozessoptimierung ist hier als Quick Check mit KVP und Lean Production integriert. Durch einen Process Flow ist die Bedienung für jeden einfach machbar. Wenn zudem per Action Cam nur die Vorgänge gefilmt werden, gibt es auch kein Problem mit dem Datenschutz oder eventuell doch sichtbare Köpfe können automatisch verpixelt werden.
Mit den Quick-Checks sind häufig schon Einsparpotentiale von mehr als 25 % möglich. Wobei die Mitarbeiter als eigentliche Experten aktiv an den Optimierungsworkshops teilnehmen sollten. Denn nur sie kennen die tatsächlichen Probleme und können geeignete Maßnahmen vorschlagen, die sie dann umsetzen.
Wenden Sie sich an uns für mehr Informationen.
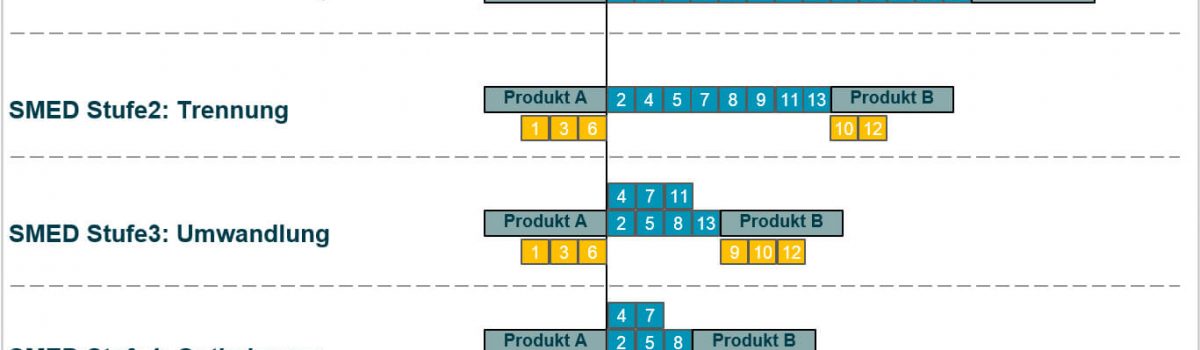
Schnelles Rüsten in der Produktion
Schnelles Rüsten in der Produktion ist wichtig, um Produktionswechsel schnell, sicher und effizient durchzuführen. Denn die aus schnellerem Rüsten resultierenden deutlichen Leistungssteigerungen an den Produktionsanlagen reduzieren Durchlaufzeiten, Losgrößen und Bestände. Dadurch lassen sich die Kosten, Flexibilität und Kundenorientierung des Unternehmens steigern.
Am effektivsten kann Schnelles Rüsten in der Produktion mit Hilfe der TimeStudy Videoanalyse umgesetzt werden. Denn sie macht Verschwendung und nicht wertschöpfende Tätigkeiten sichtbar. In einem der Videoanalyse folgenden Rüstworkshop können Mitarbeitende lernen, wie mittels technischer und organisatorischer Maßnahmen die Anlagenverfügbarkeit und somit die Produktivität erhöht wird.
Es geht darum, den Rüstprozess in internes (Maschine nicht in Betrieb) und externes Rüsten (Maschine in Betrieb) zur besseren Vorbereitung zu unterteilen. Die Mitarbeitenden lernen, dass Rüstwagen und Shadowboards den Arbeitsplatz effizienter, ergonomischer, sicherer und produktiver machen.
Dabei erleichtert ein einfaches Auswerten mit der TimeStudy-Videoanalyse inkl. Berichten und Grafiken per Klick das Besprechen der Ergebnisse und sinnvoller Maßnahmen zur Rüstzeitoptimierung im Team.
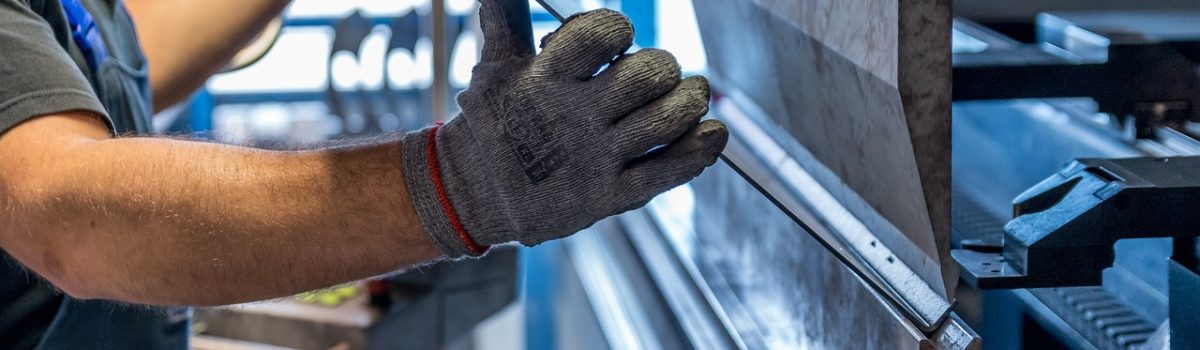
Videoanalyse mit einer ActionCam
Der Vorteil bei der Videoanalyse mit einer ActionCam ist, dass der Mitarbeiter nicht gefilmt wird, sondern selbst und nur den Prozesse filmt. Eine ActionCam ist schnell am Helm oder per Bauchgurt befestigt und einsatzbereit. Es ist also keine zusätzliche Person für die Kameraführung nötig. Denn die filmende Person kann den Einsatz über das Smartphone oder Tablet checken. Sollten doch einmal Gesichter zu sehen sein, kann man sie mit dem TimeStudy-Tool verpixeln.
Vorgehensweise bei der Videoanalyse
Ein Mitarbeitender filmt die eigenen Tätigkeiten für die Videoanalyse mit einer ActionCam. Anschließend werden am Computer mit TimeStudy T1 die Zeiten gemessen. Die Zeittreiber, wertschöpfende und nicht wertschöpfende Prozesse kann man so schnell identifizieren. Mit den Mitarbeitenden bespricht die verantwortliche Person die gefilmten Prozesse. Sie diskutieren dann gemeinsam problematische Abläufe, um daraufhin Maßnahmen zu überlegen. Jedem Messwert können sofort Ideen und Maßnahmen zur Optimierung des Ablaufs zugeordnet werden.
Um die Analyse grafisch darzustellen, können Sie z. B. Treppenstufendiagramme nutzen, die die Potenziale darstellen. So lassen sich mit Hilfe der TimeStudy T1 Videoanalyse mit einer ActionCam schnell Potentiale ermitteln, die daraufhin in die Praxis umzusetzen sind.
Einmal standardisierte Abläufe sollten Sie in einer Arbeitsanweisung festhalten, die Sie mit dem TimeStudy-Programm auch visualisieren können. Oder Sie erstellen gleich Lehrfilme bzw. Tutorials zur Standardisierung der Prozessabläufe, die sie automatisch übersetzen und unternehmensweit einsetzen können.
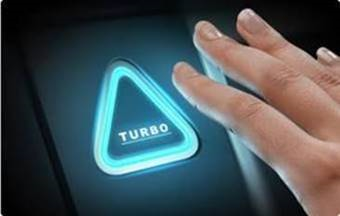
TimeStudy Turbodatenermittlung
Mit der TimeStudy Turbodatenermittlung kommen Sie besonders schnell und effektiv an wichtige Zeit-, Kalkulations- oder SAP-Daten. Denn diese können die Grundlage für Ihre Fertigungszeiten bilden, solange die Daten nicht entlohnungsrelevant sind. Der Vorgang belastet die Mitarbeitenden kaum, da der Zeitnehmer nur kurz anwesend ist. So werden zudem die entstehenden Kosten für das Unternehmen besonders niedrig gehalten. Der große Vorteil ist, dass mit wenig Aufwand viele Prozesse schnell analysiert und ausgewertet werden können.
Die Art der TimeStudy Turbodatenermittlung ist daher kostengünstig und bindet kaum Kapazitäten im Unternehmen, denn wenige Messwerte genügen. Die Daten für die Kalkulation oder Vorgabezeiten für das ERP-/PPS-System (z.B. SAP) sind mit der TimeStudy Videoanalyse schnell ermittelt und ausgewertet. Sie können die Aufnahmen natürlich sowohl selbst durchführen und uns zuschicken als auch von uns durchführen lassen. Während der Analyse verpixeln wir ggf. erkennbare Gesichter direkt, so dass datenschutzrechtliche Bestimmungen eingehalten werden können. Der Betriebsrat wird selbstverständlich vorher entsprechend informiert.
Bei der Auswertung unterscheiden wir, welche Prozessbestandteile notwendig sind oder entfallen könnten und welche verändert und optimiert werden sollten. Durch diese detaillierte Auswertung erhalten Sie von uns eine anschaulich dokumentierte Schwachstellen-Analyse. So können die nicht-wertschöpfenden, unproduktiven Zeitanteile im Prozess gezielt bestimmt und eliminiert werden.
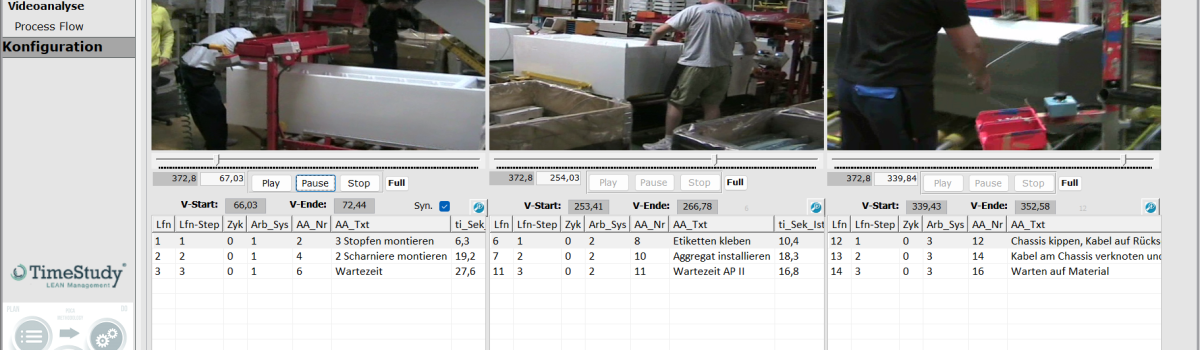
Austaktung von Arbeitssystemen
Die Austaktung von Arbeitssystemen ist nach der Prozessanalyse mit der TimeStudy T1 Videoanalyse für drei Arbeitsplätze gleichzeitig möglich. Sie können drei Prozessabläufe auswählen und diese im Parallellauf darstellen. Dadurch können Sie die Abläufe genaustens abgleichen und Ihre Montagelinien austakten.
Zu allen drei Arbeitssystemen werden Einzelzeiten und Wertschöpfungsanteile zu jedem Prozessschritt sowie die Summe der Prozesszeiten dargestellt. Sie können einzelne Prozessschritte von einem auf den anderen Arbeitsplatz verschieben, um die Auslastung anzupassen.
Über den in TimeStudy T1 integrierten Excel-Exportkonfigurator können Sie alle Daten in ein Yamazumi- oder Taktungsdiagramm exportieren.
Melden Sie sich bei uns. Gerne geben wir Ihnen weitere Informationen zur Austaktung von Arbeitssystemen.
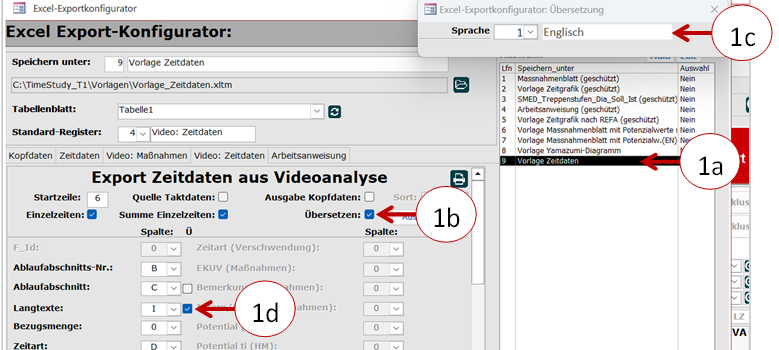
Automatische Übersetzung von Anweisungen
Die automatische Übersetzung von Anweisungen wie z. B. Arbeitsanweisungen erleichtert unternehmensweites Arbeiten und zur Verfügung stellen von Informationen ohne Zeitverlust.
Nach Zeitaufnahmen oder Videoanalysen können Sie die hinterlegten Informationen über den Excel-Exportkonfigurator automatisch übersetzen lassen. Die Definitionen der Ablaufabschnitte oder die dazugehörigen Langtexte können wahlweise durch den Google- oder Microsoft-Translator übersetzt werden. Dies ist besonders hilfreich bei der Erstellung von Arbeits-, Montage- oder Rüstanweisungen usw., wenn die Dokumente in mehrere Sprachen übersetzt werden müssen.
Sie wählen die gewünschte Vorlage aus, klicken Sie auf Übersetzen, dann öffnet sich ein Popup-Fenster zur Auswahl der Sprachen. Wählen Sie die gewünschte Sprache aus. Sie können zwei Datenfelder für den Export auswählen: Ablaufabschnitt und Langtexte.
Gerne informieren wir Sie über dieses Feature. Nehmen Sie Kontakt mit uns auf.
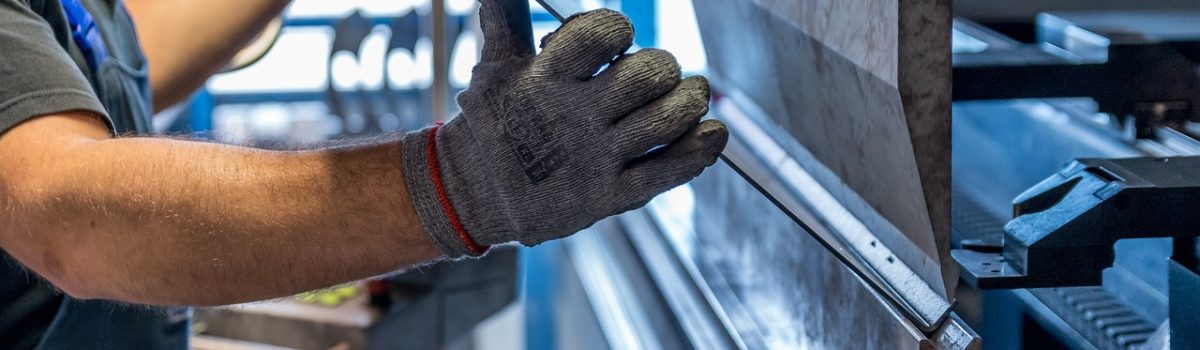
SMED – Rüstzeitoptimierung
Sie möchten mit SMED – einer Rüstzeitoptimierung – Anlagenstillstände minimieren, Rüstprozesse standardisieren, Kunden dadurch schneller und flexibler bedienen können, die Losgrößen und Bestände optimieren und die Mitarbeiter qualifizieren? Dann ist ein SMED – Workshop sinnvoll.
Besonders, wenn dabei die Videoanalyse zum Einsatz kommt, ist eine Information der Mitarbeiter im Vorfeld des Workshops zur Klärung aller Fragen und Bedenken unabdingbar. Denn die Mitarbeiter sollten genau wissen, worum es bei der Videoanalyse und bei SMED geht, damit die Maßnahmen nachhaltig implementiert werden können.
Beim Rüsten müssen alle Handgriffe perfekt aufeinander abgestimmt sein. Und alles, was dabei außerhalb der Maschine vorbereitet werden kann, dient dazu, unproduktive Standzeiten zu verringern.
Vorbereitung Workshop SMED – Rüstzeitoptimierung
Vor Ort sind zuerst die genauen Abläufe des zu betrachtenden Rüstvorganges zu erläutern, so dass alle Teilnehmenden des Teams den Rüstvorgang verstehen können.
Das Team sollte auch checken, wie die Planung und der Anstoß des Rüstvorgangs abläuft:
- Gibt es Arbeitspapiere?
- Wer erstellt diese?
- Wie viel Vorlauf ist zu erkennen?
- Wer gibt wie und wann den Auftrag zur Umrüstung?
Unbedingt die Vorbereitung zum Rüsten betrachten:
- Bereitstellung der Rüstwerkzeuge
- Wegfahren von altem Produktionsmaterial und Halbzeugen
- Holen von neuem Produktionsmaterial und Halbzeugen
Kontaktieren Sie uns für weitere Informationen.
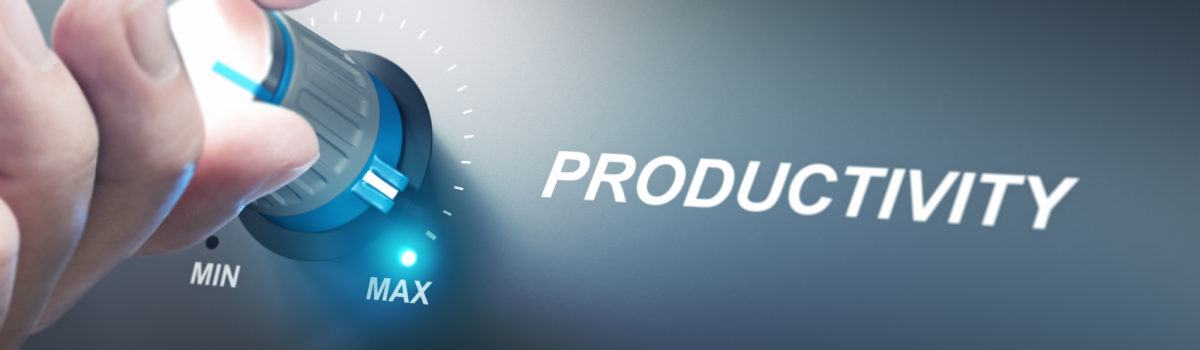
Rüstzeitoptimierung per Videoanalyse
Eine Rüstzeitoptimierung per Videoanalyse ist der Schlüssel zu geringeren Beständen, kürzeren Durchlaufzeiten, mehr Flexibilität und Wettbewerbsfähigkeit. Mit standardisierten Abläufen reduzieren Sie Fehler und senken Herstellkosten.
Rüstzeitoptimierung per Videoanalyse – ein Schritt zu besserer Wettbewerbsfähigkeit
Sie steigern durch SMED (das Schnelle Rüsten) die Maschinenverfügbarkeit und erreichen durch diese Rüstzeitoptimierung eine Prouktivitätssteigerung von mindestens 30% ohne zusätzliches Personal einzusetzen. Somit werden die Kosten gesenkt, die Lieferzeiten verkürzt, die Qualität verbessert und die Umlaufbestände reduziert. Dazu nutzen Sie technische und organisatorische Maßnahmen. Hier erweist sich die Videoanalyse als besonders hilfreiches Tool, um Schwachstellen und Verschwendung im Produktionsprozess zu visualisieren. Nach Implementierung der Gegenmaßnahmen erreichen Sie Leistungssteigerungen in der Produktion, reduzieren Durchlaufzeiten, Losgrößen und Bestände, Sie steigern die Flexibilität und Kundenorientierung.
Nachfolgende Optimierungsansätze zeigen Ihnen Beispiele für zu ergreifende Maßnahmen:
- Unterteilen des Rüstprozesses in internes (Maschine nicht in Betrieb) und externes Rüsten (Maschine in Betrieb) zur besseren Vorbereitung.
- Einsatz von Rüstwagen und Shadowboards (passend abgestimmte Werkzeugvorlagen zur gezielten und schnellen Auffindbarkeit), um den Arbeitsplatz effizienter, ergonomischer, sicherer und damit produktiver zu gestalten.
- Berichte und Grafiken mit der Videoanalyse auf Knopfdruck erstellen, um sie der Geschäftsleitung und anderen Abteilungen vorzulegen.
Natürlich ist es bei der Rüstzeitoptimierung per Videoanalyse wichtig, von Beginn an das gesamte Team und den Betriebsrat ins Boot zu holen, auch, um im Folgenden die Nachhaltigkeit zu sichern.
Wenn Sie es wünschen, sind wir Ihnen dabei gerne behilflich. Sprechen Sie uns an – Telefon: 02306 / 9254 000 oder schreiben Sie uns.
Lean Management Methoden
Lean Management Methoden werden eingesetzt, um kontinuierliche Verbesserungen, z. B. durch schlankere Prozesse zu erreichen. Das heißt Produktionsabläufe sollten transparent, effizient und wirtschaftlich gestaltet sein, um sowohl den Kundenanforderungen als auch dem unternehmerischen Wandel genüge zu tun ohne dabei die Mitarbeiter außen vor zu lassen.
Ziele von Lean Management Methoden:
- Steigerung der Produktivität/Durchlaufzeiten durch erhöhte Anlagenverfügbarkeit
- Reduzieren von Maschinenstillstandszeiten
- Senken der Produktionskosten
- Reduzierung von Verschwendungen durch mehr wertschöpfende Anteile im Arbeitsprozess
- Erhöhen des Umsatzes, Gewinns und der Wettbewerbsfähigkeit
Zwei Beispiele für Lean Management Methoden:
Eine dieser Methoden ist 5S / 6S – die sichere, saubere, übersichtliche und standardisierte Gestaltung der Arbeitsplätze. Durch 5S / 6S verbessern Sie grundlegend die Arbeitsprozesse und senken das Risiko von Arbeitsunfällen spürbar. In zudem ergonomisch optimierten Arbeitsplätzen und standardisierten Abläufen steckt sogar noch mehr Potential.
Daraus ergibt sich eine weitere Möglichkeit – SMED (Single Minute Exchange of Die), das Austauschen von Vorrichtungen an Maschinen im einstelligen Minutenbereich. Denn eine perfekte Vorbereitung, Standardisierung und Strukturierung des Ablaufs sowie eine klare Rollenverteilung minimieren die Dauer des Rüstablaufs und erhöhen die Maschinenverfügbarkeit (OEE). Dazu unterteilt man die Rüstprozesse in internes (Maschine nicht in Betrieb) und externes Rüsten (Maschine in Betrieb), damit man sie besser vorbereitet kann.
Wichtig für die erfolgreiche Umsetzung der Lean Methoden ist die Bereitschaft von Unternehmensführung und Mitarbeitern, sich auf einen Wandel in der Unternehmenskultur hin zu mehr Transparenz, Team- und Kundenorientierung sowie Wertschätzung einzulassen. Alle sollten diesen Weg mitgehen können, damit es einen nachhaltigen Nutzen gibt.